Don't
risk lost-time accidents!
Increase safety with
automated OSHA checklists for
forklift and other
mobile equipment operators. Automated wireless OSHA
Checklists ensure that each operator verifies that all
critical mobile equipment components are in proper operating
condition at the start of each shift. Reduce maintenance
cost while improving safety! Takes just a few seconds each
day. Centralized database allows detailed analysis and
record archiving.
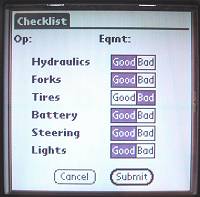 |
OSHA Checklist
Palm-based handheld solution for forklift and other mobile equipment
checklists.
|
Detailed Features
-
Allows
operators to quickly and easily verify correct operation
of all systems on forklift or other equipment items at the
beginning of each shift, allowing full compliance with
OSHA safety regulations.
-
Can be used
to pre-authorize operators to use equipment, based on
their individual
certifications and training.
-
Collects
operating hours for each forklift or other equipment for planned maintenance
scheduling.
-
Collect
specific
repair needs, to schedule maintenance and keep equipment in optimal
condition.
-
Data is
returned to a central PC for collection of checklists,
dispatching of repairs, and planned maintenance.
-
Includes
comprehensive PC-based program to enter operator names,
equipment types, checklist items, repair items, training
records, etc.
-
Runs
on Symbol™ factory-hardened
handhelds,
or any Palm OS compatible device. Can also be integrated
with barcode scanning software for inventory, reading
employee badges,
location tracking, maintenance, etc.
-
Priced
individually, by location, or by company (customization
services available to interface with existing CMMS
systems).
-
Detailed
reports for planned maintenance, utilization, safety records,
repair history, and many others.
-
Can be
fully customized or productized for forklift or other mobile equipment manufacturers
such as Mitsubishi, Crown, Raymond, Hyster, Clark, Toyota,
Yale, etc.
OSHA 29CFR 1910.178(q)(7)
requires that appropriate safety checks are completed at the
beginning of each shift. Now you can verify full compliance.
Improve safety, reduce repair times, and reduce liability by
ensuring that EVERY piece of mobile equipment is adequately
inspected before use.
In
addition, overall fleet maintenance is greatly enhanced by tracking
actual hours of operation for each piece of equipment.
Planned mainte-nance reduces overall operating costs, and
reduces the likelihood of accidents.
Contact
Us today for pricing.
 Click for more
sample projects |